Case Study: Oil Refinery Operator + Lincoln Electric Additive Manufacturing

Accelerating Routine Maintenance Timelines with WAAM Parts from Lincoln Electric
Stress Engineering Services (SES), a leader in qualification and testing, partners with industry leaders across aerospace, defense, medical, energy, nuclear, and automotive sectors. When a domestic oil refinery operator faced a significant halt in production due to equipment failure, they looked at 3D printed additively manufactured (AM) parts as an alternative option for replacing the component. After designing the replacement themselves, the operator partnered with Lincoln Electric to quickly produce the part using Wire Arc Additive Manufacturing (WAAM). To further expedite the maintenance period, the operator and Lincoln Electric connected with SES to perform full-scale product validation tests to qualify the replacement component.
Challenge
During routine inspection, a critical component at the refinery was found to have several relevant indications warranting replacement prior to continued service. The OEM part, a casting originally made from high grade nickel alloy, was challenging to replace due to its unique composition and the long lead times associated with traditional manufacturing methods. Ongoing supply chain issues and a lack of skilled labor resulted in a lead time of at least 3-months for the internationally manufactured replacement component. As part of the manufacturing and inspection process, the part is subjected to a rigorous qualification process that can take months. The urgency of the situation was compounded by the potential downtime, which threatened significant production losses.
Solution
Having previously explored options for 3D additively manufactured components, the operator chose to use the WAAM process for the replacement part, which offered an expeditious and flexible design and manufacturing alternative. The operator took the lead in optimizing the design, while Lincoln Electric, with its comprehensive welding technology capabilities, managed the manufacturing. As a vertically integrated company, Lincoln Electric could provide not only the technology to sculpt the component to near net shape at their facility in Cleveland, OH, but also the material and machine capacity with which to build it. Part of the advantage of WAAM was in its use of alternative material that was more readily available and well suited for the specific application. The original component was installed using welds consisting of a traditional nickel alloy. As a proven material for petroleum applications, this alloy became an obvious choice for the replacement component.
SES’s advisory expertise contributed to the navigation of the product inspection and validation testing processes, ensuring the new component met all industry standards for the unique intended service application. Our involvement ensured the part’s design was optimized for testing, leveraging our extensive experience across various industries to bridge the gap between theoretical design and practical application.
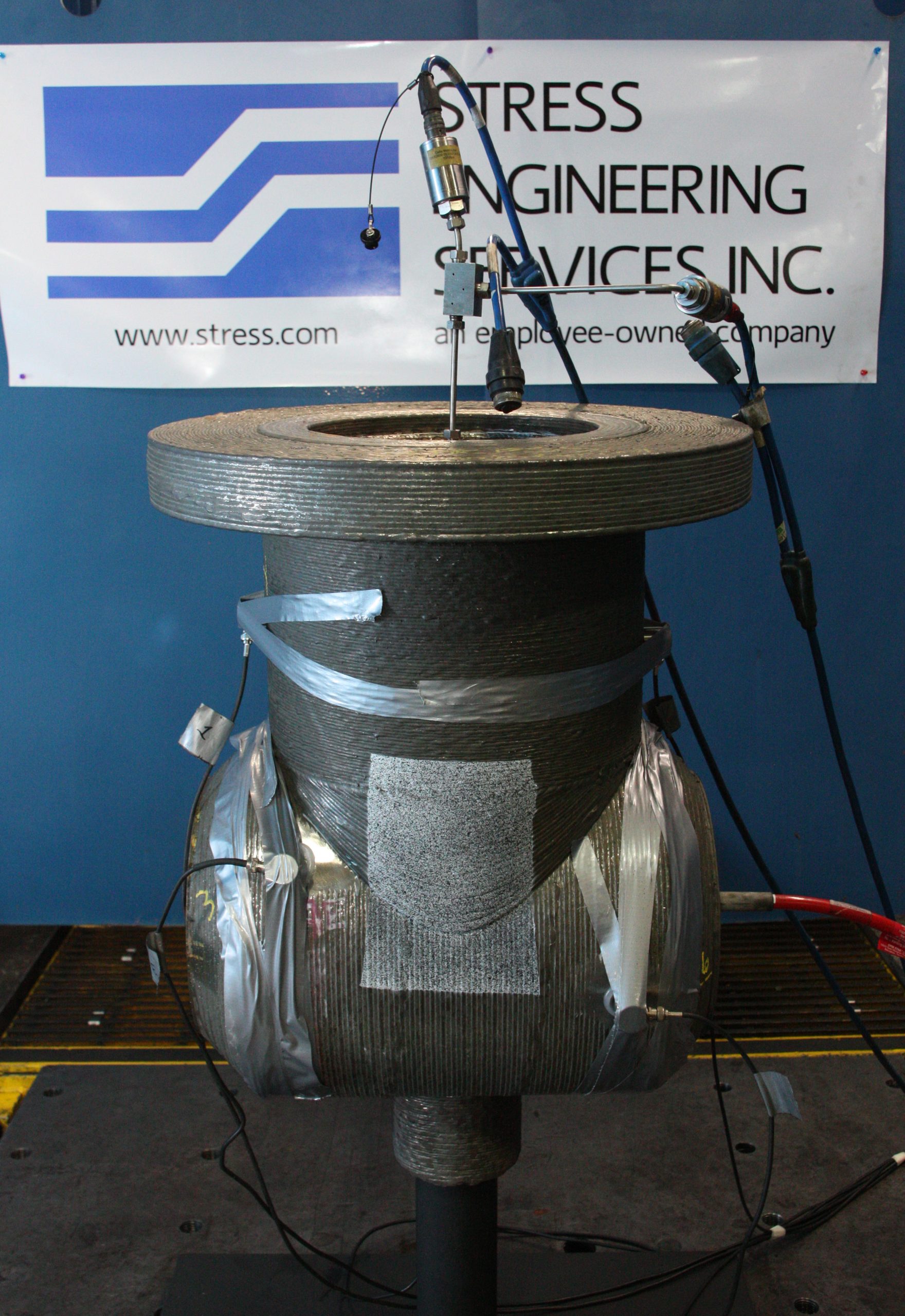
Our role was to perform full-scale product validation testing to confirm that the replacement part was suitable for its intended application, based upon the specified engineering requirements. The collaborative effort was streamlined through our development of a comprehensive test strategy based on the functional specification for the component, enabling parallel progress in manufacturing and test planning phases. While Lincoln Electric was 3D printing the new component, we designed and manufactured the carbon steel end cap test fixtures, using the dimensions provided by the operator and Lincoln Electric. Through our knowledge of the pressure and other critical factors to the application and qualification test requirements, we were able to quickly produce these fixtures and qualify the required welding procedure to ASME with our in-house test engineering design team, welding engineering support staff, welders, and machinists.
This approach was instrumental in expediting the qualification process, ensuring the part adhered to stringent industry standards; American Petroleum Institute (API) 20S and ASME Section IX QW-600. Once we received the manufactured component, we performed a comprehensive inspection according to standard engineering design requirements, as well as the operator’s requirements. Conventional dimensional inspection methods were supplemented with SES’s 3D metrology scanner to capture the as-built dimensions on the outer diameter, while a SES laser scanner captured the inner diameter dimensions. Next, we completed a nondestructive examination of the new header to verify its integrity with a traditional liquid penetrant surface test and a volumetric ultrasonic examination of critical locations on the part body. Then, we installed the end plug test fixturing for functional qualification.


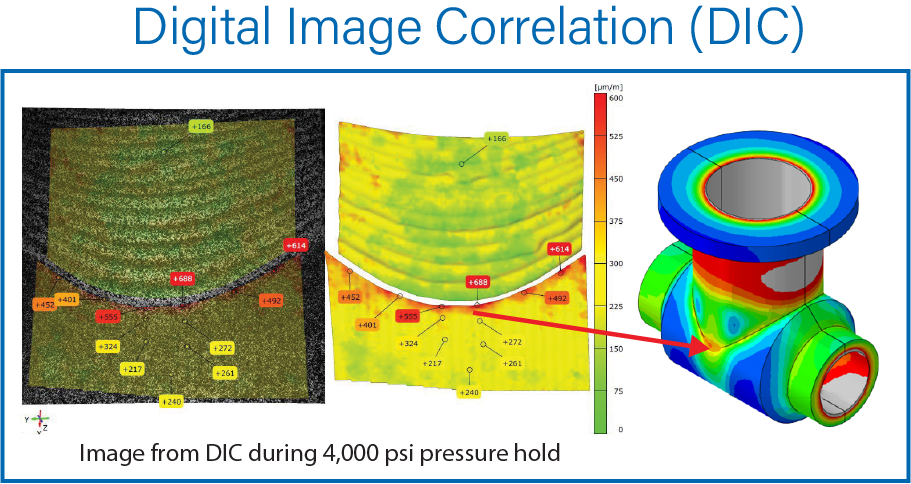
In addition to pressure testing, we employed digital image correlation (DIC) and acoustic emission (AE) testing to further verify the integrity of the nickel alloy component. DIC, is a 3D, full-field, optical technique used to measure deformation and strain on material via tracking of grey value patterns in neighboring subsets (facets) found on the supplemental coating applied at SES.
When the full-scale component was subjected to the loads during the pressure loading validation test. DIC is a nonintrusive test that helps to confirm the finite element analysis (FEA) model and anisotropy of the component. Our AE testing similarly confirmed the integrity of the material using probes to monitor any release of energy that warns of potential failure. AE can detect and locate changes in the material during the test program and validate the stability in a given condition.
Results
The collaboration between the operator, Lincoln Electric, and SES drastically reduced the anticipated downtime from four months to just four weeks. This achievement not only demonstrated the practical benefits of WAAM technology but also highlighted SES’s ability to accelerate the testing and qualification process through efficient parallel development. The successful implementation and operation of the part underscored SES’s commitment to delivering high-quality solutions under urgent timelines.
Transform Your Manufacturing Process
This case study underscores SES’s expertise in leveraging additive manufacturing technologies to provide timely, cost-effective solutions for critical engineering challenges. It highlights our capacity to navigate complex regulatory environments and deliver qualified components that meet precise industry and client standards.
Explore how SES’s 3D printed additive manufacturing testing services can benefit your operations. Contact us to discover more about our capabilities and how we can assist in transforming your manufacturing processes with innovative solutions.

Award Winning Technology
The team of Lincoln Electric, Stress Engineering Services, and Chevron received the prestigious 2023 TCT Award in the Industrial Product Application category for 3D metal printing refinery pressure components. The TCT Awards celebrate advances in technology, innovation and collaboration in the global 3D printing and additive manufacturing industry. The team collaborated to qualify and manufacture pressure components that were installed in a hydrogen furnace at a Chevron refinery.
Leave a Comment
You must Register or Login to post a comment.