The True Value of Subsea Emergency Pipeline Repair Systems
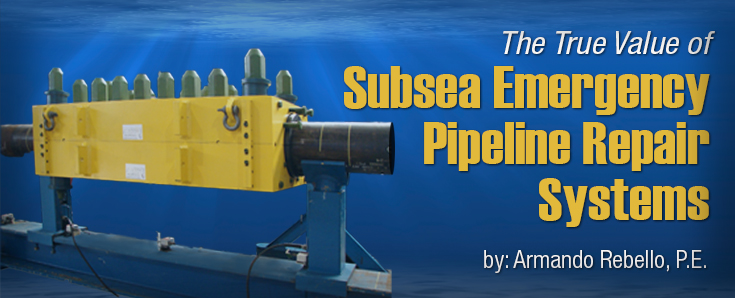
The consequences of subsea pipeline emergencies can often be catastrophic, both environmentally and financially. A large, uncontrolled pipeline breach has the potential to financially devastate a company, causing them to face long-term loss of revenue, crippling environmental remediation costs, liabilities and fines, not to mention the immeasurable cost of a damaged company reputation.
Thankfully, these events are relatively rare, but emergency pipeline repair systems (EPRS) are playing an increasingly vital role in the industry for pipeline operators keen on avoiding any potential trouble down the line.
There is no doubt about it – owning an EPRS requires a serious allocation of CAPEX, associated procurement time and ongoing maintenance costs. Incurring these types of expenditures on a system that – if all goes well – may never be used, can understandably cause some operators pause for thought. However, the risk of such an emergency occurring should not be dismissed, and event probability only increases over time.
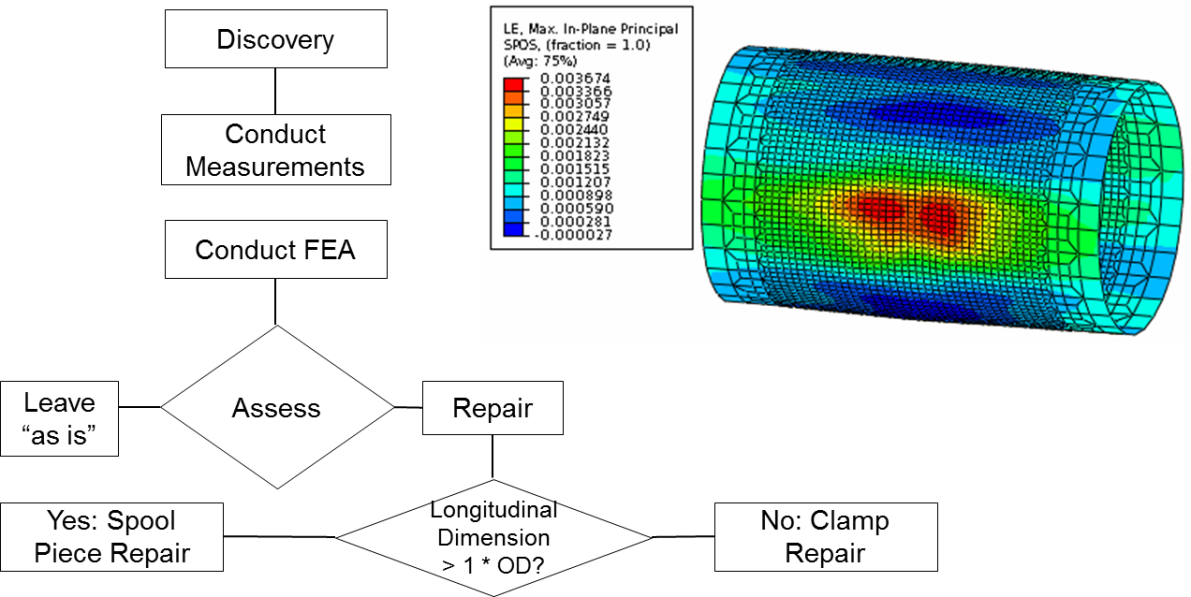
The cost of implementing an EPRS represents just a fraction of the costs of an unsupported emergency pipeline event, and allows for tooling and equipment to be available for immediate use, versus procurement schedules that can last well over a year. Across the industry, attention must be paid to plugging the gap in pipeline support activities perceived as ‘non-essential’ and additional consideration given to asset sharing organizations, which are growing in popularity. In Asset Sharing Organizations (ASOs) co-owners join together to share the CAPEX and maintenance costs and commit to a core mission of ‘readiness for emergency repairs’ – allowing member operators to focus on their own core businesses.
EPRSs are not just a collection of tools. They are logistic organizations devoted to emergency pipeline repairs. They have maintenance programs and mobilization procedures in place, along with regular training programs which involve coordination with operators, vendors, offshore intervention contractors, etc.
Depending on regional factors, repair systems are either diver assisted or diverless (installed by remotely operated vehicles or ROVs). The mobilization of a diverless EPRS is more complex than a diver assisted system, with larger equipment being loaded on intervention vessels.
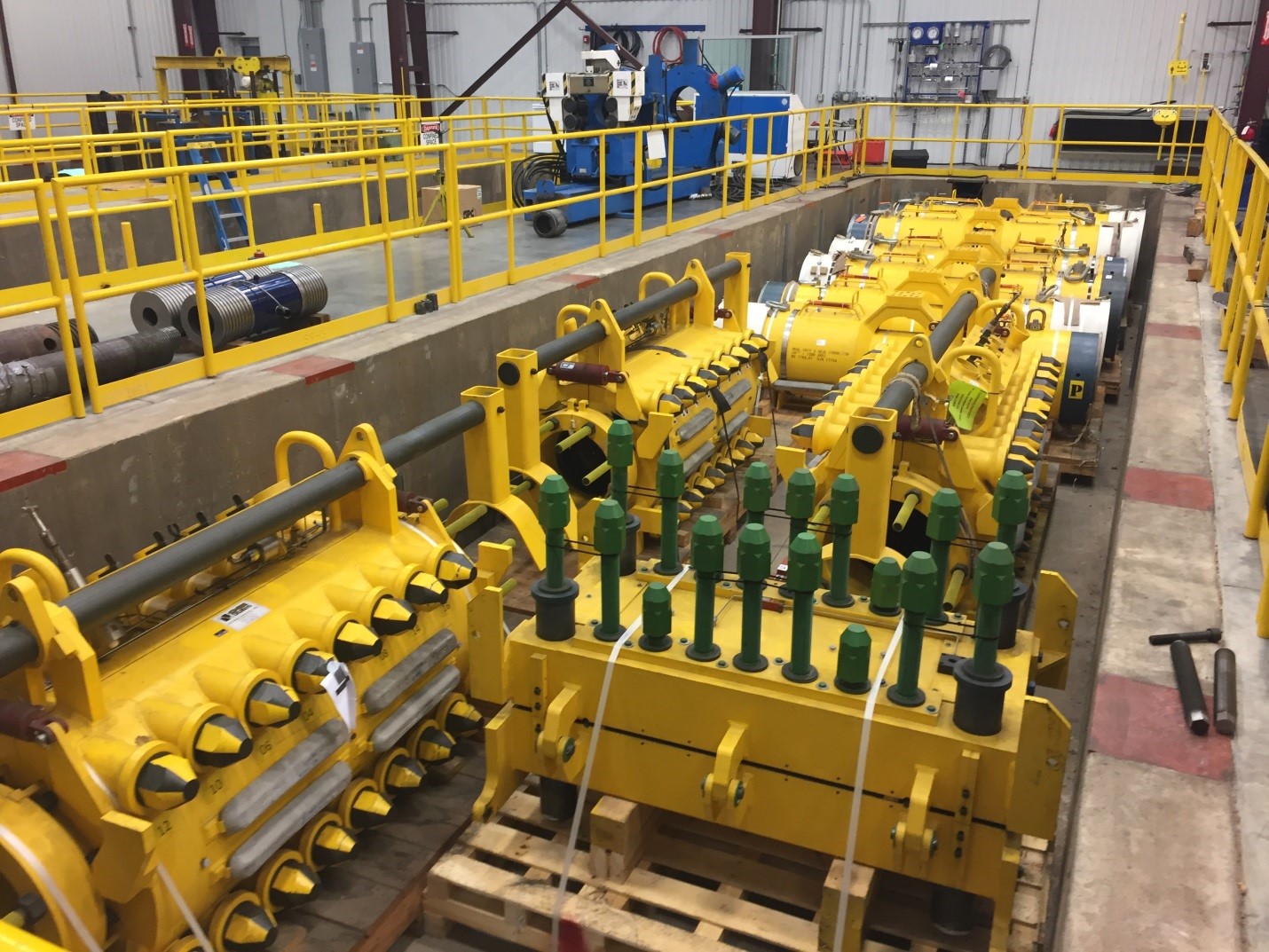
Forming an EPRs may start with the following steps:
- Consider the pipeline network your company owns, list diameters, design pressures, operating temperatures, steel grades, type of external coatings and wall thicknesses;
- Contract a reputable engineering firm to define the resources required to perform emergency repairs, along with budgetary costs and procurement schedule;
- Define failure modes and consequences (usually through a failure mode, effects and criticality analysis) – Identify common threats to the pipeline(s);
- Estimate the time to conduct repairs in the event of a failure: Consider the loss of revenue and cost to expedite delivery of tools and equipment;
- Decide if an EPRS is necessary.
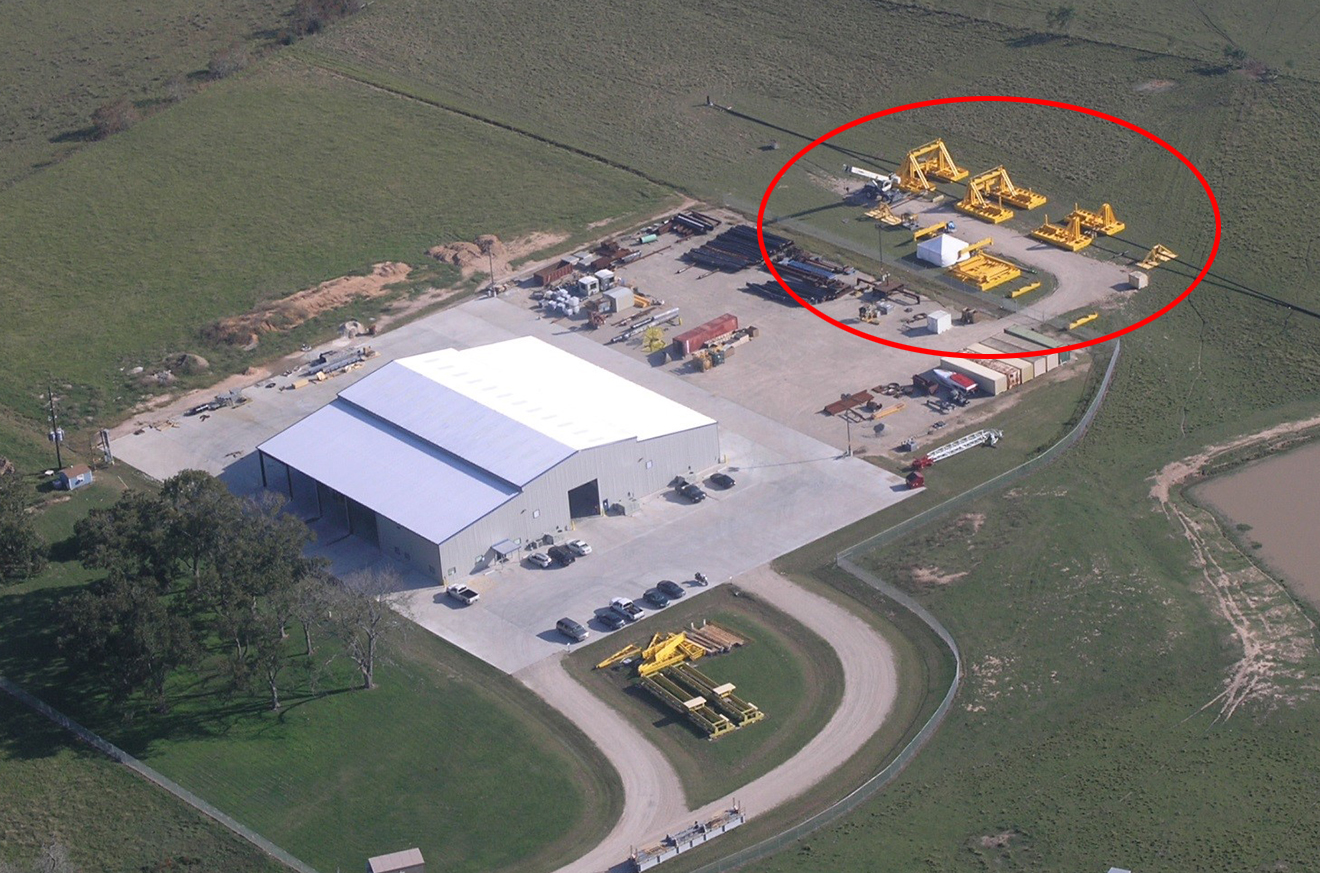
Conclusion
Contrary to general perception, EPRSs are organizations dedicated to the management of pipeline repair inventory, repair engineering, logistics and procurement, all under a single roof so an emergency is dealt with in a coordinated manner and without loss of precious time.
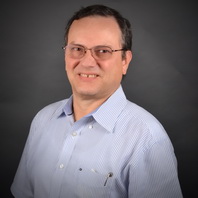
Armando Rebello, P.E. – Sr. Associate, Houston Office
Since 2003, Armando has been a essential member of the Upstream Group at Stress Engineering Services. He has spent the past 34 years of his career in the field of offshore pipeline installation, manufacturing and project management in the U.S. and overseas, including 16 years of direct work with flexible pipelines and risers. He graduated with a BS is mechanical engineering and is also a registered professional engineer in the state of Texas.
Leave a Comment
You must Register or Login to post a comment.